OTTO-CHEMIE
Partner: OTTO-CHEMIE, Standort: Fridolfing
Von außen stechen nur die zwei silberfarbenen Metallsilos ins Auge, die dem nüchternen weißen Gebäude ein wenig Glanz verleihen: Doch im Inneren läuft die Produktion dank evon XAMControl voll digitalisiert nach Industrie 4.0-Standard.
Ein geschlossenes System von der Anlieferung bis zur Abfüllung für die OTTO-Dichtstoffe
Die Hermann Otto GmbH, kurz OTTO, ist ein 1881 gegründetes bayrisches Traditionsunternehmen. Seit den 1960er Jahren werden Silikon-Dichtstoffe und Klebstoffe auf Basis von Silikon, Polyurethan, silanterminierten Polymeren (Hybrid) und Acrylaten entwickelt und vertrieben.
Im neuen Werk in Kaltenbrunn werden die beliebten Dichtstoffe von OTTO hergestellt, denn bei diesen Produkten mit hohen Mengen kommt die Produktivität der Hightech-Anlage auf Basis von evon XAMControl voll zum Tragen. Die Herstellung erfolgt nahezu vollautomatisch und in einem geschlossenen System. Im Gegensatz zur bisherigen Produktion, die nach wie vor am Standort Krankenhausstraße in kleineren Chargen und mit vergleichsweise hohem Mitarbeitereinsatz für die einzelnen Arbeitsschritte abläuft. In Kaltenbrunn werden die Grundstoffe aus den Vorratsbehältern, also das Polymer aus dem Tank und die Kieselsäure aus dem Silo, automatisch dosiert und dem Mischbehälter zugeführt. Die Zugabe von Additiven und Farbpigmenten für die jeweilige Produktfarbe erfolgt über einen Statikmischer in der Abfüllstrecke der Kartuschen. Ebenso wie das Abfüllen erfolgt die Bedruckung, Verpackung in Kartons und die Palettierung durch einen Roboter vollautomatisiert.
Das Herzstück: Das Prozessleitsystem evon XAMControl
Damit die Produktion reibungslos und immer in der gleichen Qualität erfolgt, spielt die Verknüpfung von Elektronik, Software und den Maschinen selbst eine maßgebliche Rolle. Zur Überwachung und Steuerung aller Prozesse der vollautomatisierten Anlage entwickelten Spezialisten von evon gemeinsam mit den Verantwortlichen von OTTO ein maßgenaues Prozessleitsystem auf Basis von evon XAMControl. Über einen digitalen Leitstand, bei dem der ganze Produktionsprozess und die Daten dahinter visuell abgebildet werden, erhält der Produktionsleiter Einblick in die laufenden Vorgänge, kann bei Störungen die Fehlerquelle exakt orten und im Notfall auch steuernd eingreifen. Durch die Aufzeichnung der Daten lassen sich die Prozesse ebenso überwachen, wie auch analysieren bzw. rückverfolgen. Wesentlicher Bestandteil für die Produktion sind die integrierten Wartungspläne und die Alarmierung bei Fehlern (SMS, E-Mail).
Neben der Produktion sind aber auch die Gebäudeautomation und die Logistik im Prozessleitsystem von evon XAMControl integriert. Das bietet eine Reihe von Vorteilen: Auf der einen Seite für den Bereich der Logistik, da die Bestandsüberwachung mehr Sicherheit in der Produktion bringt und die Kommissionierung mit Tablets und Handhelds eine lückenlose Nachverfolgung garantiert. Auf der anderen Seite kann neben der Produktion die komplette Erzeugung der Versorgungsmedien (Heizung, Kühlung, Druckluft u.a.) für den Standort und den Prozess in einer gemeinsamen Softwarelösung überwacht und angesteuert werden
evon XAMControl kommuniziert auch in Echtzeit mit dem ERP-System von OTTO. Das ist für die gesamtunternehmerische Planung und Steuerung zuständig: Vom Einkauf über die Lagerhaltung, das Bestellwesen und die Auftragsabwicklung bis hin zum Rechnungswesen.
evon XAMControl unterstützt, der Mensch bleibt der Macher
Die Vorteile dieses geschlossenen Systems liegen auf der Hand und sind ebenfalls klares Ziel von Industrie 4.0, denn durch die Automatisierung tritt weder der typische Essiggeruch der sauer vernetzenden Grundstoffe noch eine Staubbelastung durch die Kieselsäure in ihrem Trockenzustand auf. Diese sonst unvermeidlichen Nebeneffekte der Produktion sind zwar nicht gesundheitsschädlich, jedoch unangenehm für die Mitarbeiter und Mitarbeiterinnen. Darüber hinaus entfällt ein Großteil der körperlich schweren Arbeiten bzw. wird maßgeblich durch Maschinen unterstützt. Das OTTO-Team kann sich ab sofort ganz
auf die Qualitätssicherung konzentrieren. Und das Team bleibt unentbehrlich: Zur Vorbereitung vorproduzierte Farbpigmentmischungen und zur Bereitstellung der Dichtstoffe für die jeweilige Produktionslinie. Beim Farbabgleich ist trotz des Einsatzes eines optischen Spektrometers immer noch das geübte menschliche Auge gefragt. Die Mitarbeiter von der Qualitätskontrolle vergleichen dabei Proben der aktuellen Charge mit dem jeweiligen Farbreferenzmuster. Bei allen Maschinen bleibt also am Schluss immer noch der Mensch der Macher. Insgesamt ermöglicht die Integration von Industrie 4.0 im neuen Produktionswerk von OTTO ein Höchstmaß an Produktivität bei gleichzeitiger Einhaltung der eigenen hohen und gleichbleibenden Qualitätsanforderungen.
Kontakt
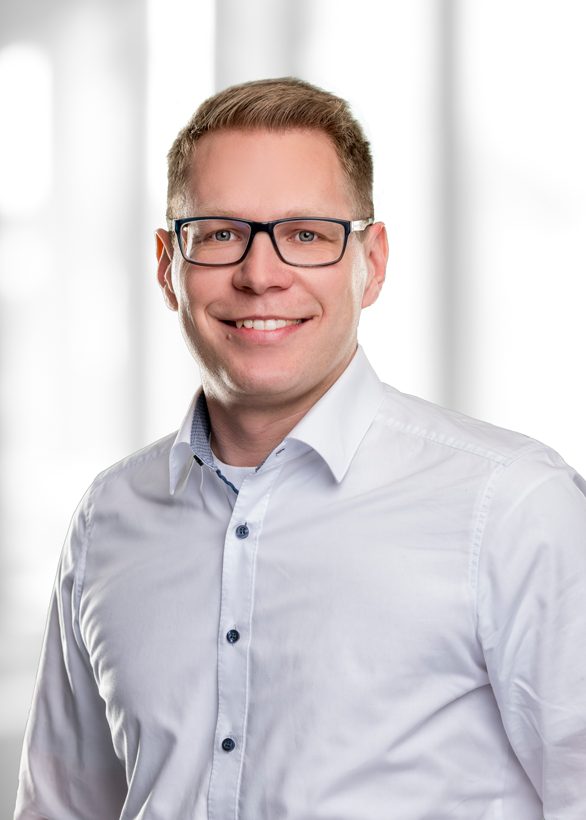
Mehr zu den evon Produktionsleittechnik-Projekten?
Gleich Formular ausfüllen oder Rene Hirschmugl anrufen!